ufabet 678 หยุดฝันแล้วลงมือทำ เปิดโอกาสให้คุณเปลี่ยนทุกวันธรรมดาให้กลายเป็นวันที่ตื่นเต้น เร้าใจ
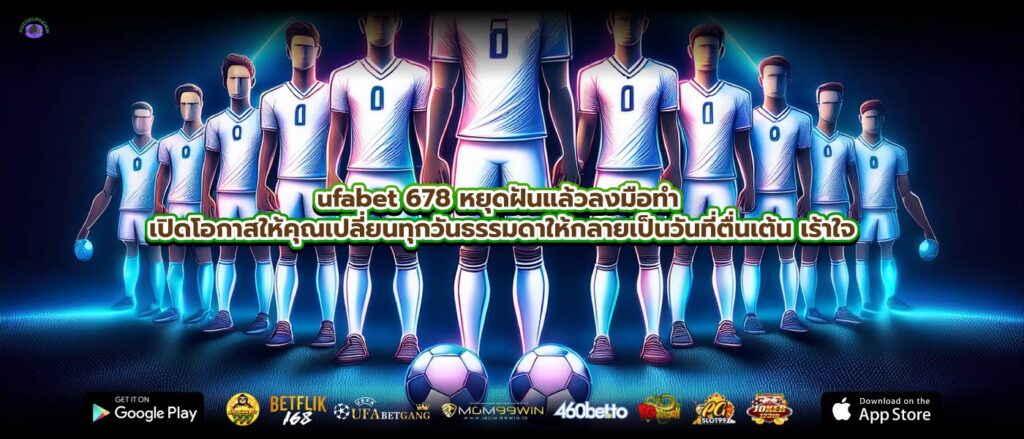
ufabet 678 แพลตฟอร์มนี้เปิดโอกาสให้ผู้ใช้สามารถเปลี่ยนแปลงวันธรรมดาให้กลายเป็นวันที่ตื่นเต้นและเร้าใจ ด้วยการนำเสนอเกมพนันที่หลากหลายและนวัตกรรมที่ทันสมัย Ufabet 678 ไม่เพียงแต่เป็นสถานที่พักผ่อนหย่อนใจ แต่ยังเป็นโอกาสในการสร้างรายได้และประสบการณ์ที่น่าจดจำ การลงมือทำและมีส่วนร่วมในกิจกรรมที่ท้าทายจึงเป็นกุญแจสำคัญในการเปลี่ยนแปลงชีวิตให้ดีขึ้น
ufabet 678 การเดิมพันออนไลน์ที่มีครบทั้งกีฬา คาสิโน สล็อต และเกมมากมายที่รอให้คุณมาสัมผัส
ufabet 678 แพลตฟอร์มการเดิมพันออนไลน์ชั้นนำที่นำเสนอตัวเลือกมากมายสำหรับผู้ที่ชื่นชอบกีฬา คาสิโน สล็อต และเกมต่างๆ เว็บไซต์ที่รวมเอาความสนใจที่หลากหลายเข้าไว้ด้วยกัน มอบประสบการณ์ที่ดื่มด่ำซึ่งผสมผสานความตื่นเต้นของการเดิมพันกีฬาเข้ากับความตื่นเต้นของเกมคาสิโนและสล็อตแมชชีนที่สร้างสรรค์ ผู้ใช้สามารถสำรวจโอกาสการเล่นเกมมากมาย ซึ่งทั้งหมดออกแบบมาเพื่อมอบความบันเทิงและการมีส่วนร่วมที่มีคุณภาพสูง เชิญชวนผู้เล่นให้ค้นพบโลกแห่งความเป็นไปได้ รับประกันประสบการณ์การพนันออนไลน์ที่ยอดเยี่ยมที่ปรับแต่งตามความต้องการของพวกเขา
ufabet 678 ลงทุนขั้นต่ำ แต่ลุ้นกำไรได้ไม่จำกัด ระบบปลอดภัย เชื่อถือได้ สมัครง่ายภายในไม่กี่ขั้นตอน
ufabet 678 แพลตฟอร์มนี้ได้รับการออกแบบมาพร้อมระบบรักษาความปลอดภัยที่แข็งแกร่ง ช่วยให้ผู้ใช้เข้าร่วมกิจกรรมต่างๆ ได้อย่างมั่นใจ โครงสร้างพื้นฐานที่เชื่อถือได้ช่วยสร้างความไว้วางใจ ทำให้เป็นตัวเลือกที่ต้องการสำหรับนักพนันทั้งมือใหม่และมือเก๋า การลงทะเบียนเป็นกระบวนการที่ตรงไปตรงมา โดยต้องใช้เพียงไม่กี่ขั้นตอนง่ายๆ ในการเริ่มต้น การเข้าถึงนี้เมื่อรวมกับตัวเลือกการเล่นเกมที่หลากหลาย
ufabet 678 การเดิมพันออนไลน์ที่ยิ่งใหญ่กว่าที่คุณเคยรู้จัก
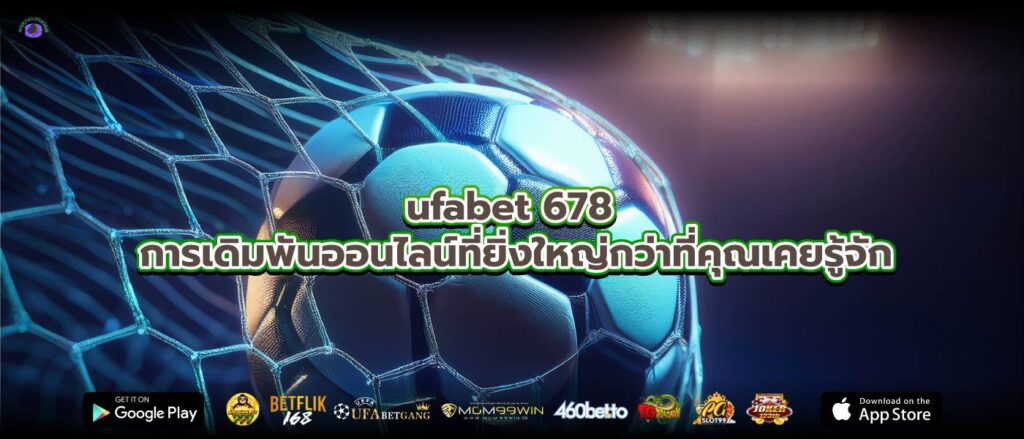
ufabet 678 แพลตฟอร์มที่นำเสนอประสบการณ์การเดิมพันที่ล้ำสมัยและครบวงจร ด้วยเทคโนโลยีที่ทันสมัยและระบบความปลอดภัยที่เชื่อถือได้ ผู้เล่นสามารถเข้าถึงเกมพนันที่หลากหลายทั้งกีฬา คาสิโนสด และเกมสล็อต ที่มีคุณภาพสูงสุด นอกจากนี้ ยังมีโปรโมชั่นและโบนัสที่น่าสนใจเพื่อเพิ่มโอกาสในการชนะและสร้างความพึงพอใจให้กับสมาชิก ด้วยการบริการที่รวดเร็วและทีมงานมืออาชีพที่พร้อมให้คำแนะนำตลอด 24 ชั่วโมง ทำให้ UFABET 678 เป็นตัวเลือกที่เหมาะสมสำหรับนักเดิมพันทุกระดับ
ufabet 678 สนุกไปกับการแทงบอลออนไลน์ที่ค่าน้ำดีที่สุดในตลาด
ufabet 678 อินเทอร์เฟซที่ใช้งานง่ายและการนำทางที่ราบรื่นทำให้เข้าถึงได้สำหรับทั้งผู้เดิมพันมือใหม่และผู้เดิมพันที่มีประสบการณ์ ด้วยตัวเลือกการเดิมพันที่หลากหลายในลีกและทัวร์นาเมนต์ต่างๆ Ufabet 678 ตอบสนองความต้องการที่หลากหลาย ส่งเสริมสภาพแวดล้อมที่น่าดึงดูดสำหรับผู้ที่ชื่นชอบกีฬา สัมผัสกับความตื่นเต้นของการเดิมพันออนไลน์พร้อมรับประโยชน์จากเงื่อนไขที่ได้เปรียบที่สุดในตลาดด้วย Ufabet 678
ufabet 678 ครบจบในที่เดียว ฝาก-ถอนออโต้ 24 ชม. ไม่ต้องรอนาน โอกาสรวยมาถึงแล้ว
ufabet 678 แพลตฟอร์มเดียวได้อย่างลงตัว ด้วยอินเทอร์เฟซที่ใช้งานง่ายและระบบฝากและถอนเงินอัตโนมัติที่ทันสมัยซึ่งพร้อมให้บริการตลอด 24 ชั่วโมงทุกวัน คุณจะสามารถเพลิดเพลินกับธุรกรรมที่ปราศจากความยุ่งยากโดยไม่ต้องรอนาน ซึ่งจะทำให้ประสบการณ์การเล่นเกมของคุณไม่สะดุด ช่วยให้คุณสามารถมุ่งเน้นไปที่สิ่งที่สำคัญอย่างแท้จริง นั่นคือการชนะ เนื่องจากโอกาสในการประสบความสำเร็จทางการเงินมีอยู่มากมายจึงเป็นตัวเลือกที่เชื่อถือได้สำหรับทั้งนักเดิมพันมือใหม่และมือเก๋า คว้าโอกาสที่จะยกระดับเส้นทางการเล่นเกมของคุณด้วยแพลตฟอร์มที่ให้ความสำคัญกับความสะดวก ความปลอดภัย และการสนับสนุนที่ไม่มีใครเทียบได้ เส้นทางสู่ความมั่งคั่งของคุณเริ่มต้นที่นี่
ufabet 678 ขอมอบความเร้าใจแบบไม่มีหยุดพัก ด้วยบริการเกมคาสิโนออนไลน์ครบทุกประเภท
ufabet 678 ให้บริการทั้งผู้เล่นมือใหม่และผู้เล่นที่มีประสบการณ์ โดยมีตัวเลือกการเล่นเกมที่หลากหลาย รวมถึงสล็อต เกมโต๊ะ และประสบการณ์ดีลเลอร์สด ด้วยความมุ่งมั่นเพื่อความบันเทิงคุณภาพสูง แพลตฟอร์มนี้จึงมีระบบนำทางที่ใช้งานง่ายและมาตรการรักษาความปลอดภัยที่แข็งแกร่ง ช่วยให้มั่นใจได้ว่าผู้ใช้ทุกคนจะได้รับสภาพแวดล้อมที่ปลอดภัยและสนุกสนาน ไม่ว่าคุณจะแสวงหาความตื่นเต้นจากการพนันที่มีเงินเดิมพันสูงหรือความบันเทิงจากการเล่นแบบสบายๆ มุ่งมั่นที่จะมอบประสบการณ์ที่ยอดเยี่ยมและน่าดึงดูดใจที่จะทำให้ผู้เล่นกลับมาเล่นซ้ำแล้วซ้ำเล่า
ufabet 678 สล็อตแตกง่าย บาคาร่า รูเล็ต เสือมังกร และอื่นๆ ที่เล่นได้ทุกที่ ทุกเวลา ลุ้นรับเงินรางวัลมหาศาลทุกวัน เล่นง่าย จ่ายจริง 100%
ufabet 678 การเล่นเกมที่ราบรื่นพร้อมตัวเลือกที่หลากหลาย เช่น สล็อต บาคาร่า รูเล็ต และเสือมังกร ซึ่งสามารถเข้าถึงได้ทุกเมื่อทุกที่ ผู้เล่นสามารถเพลิดเพลินไปกับความตื่นเต้นของการเล่นเกมพร้อมทั้งมีโอกาสชนะรางวัลเงินสดจำนวนมากทุกวัน แพลตฟอร์มได้รับการออกแบบมาเพื่อความสะดวกในการใช้งาน ทำให้ผู้เล่นทั้งมือใหม่และมือเก๋าสามารถเล่นได้อย่างสบายๆ ด้วยความมุ่งมั่นในความโปร่งใสและความน่าเชื่อถือ รับประกันการจ่ายเงินจริง 100% ทำให้ผู้ใช้สามารถมุ่งเน้นไปที่การเล่นเกมได้โดยไม่ต้องกังวลเรื่องรายได้ สัมผัสกับความตื่นเต้นของการเล่นเกมออนไลน์ที่เงินรางวัลรออยู่ทุกเมื่อ
ufabet 678 พาคุณเข้าสู่โลกแห่งการเดิมพันที่เหนือชั้น มาพร้อมกับบริการฝาก-ถอนรวดเร็วทันใจ
ufabet 678 ขอเชิญคุณสัมผัสประสบการณ์การเดิมพันที่เหนือกว่า โดยที่ทุกแง่มุมของการเล่นเกมของคุณได้รับการออกแบบมาอย่างยอดเยี่ยม แพลตฟอร์มของเราไม่เพียงแต่ใช้งานง่ายเท่านั้น แต่ยังรับประกันประสบการณ์ที่ราบรื่นด้วยบริการฝากและถอนเงินที่รวดเร็วของเรา ด้วยความมุ่งมั่นในการมอบความสะดวกสบายที่ไม่มีใครเทียบได้ เราจึงให้ความสำคัญกับเวลาและความพึงพอใจของคุณ ช่วยให้คุณสามารถมุ่งเน้นไปที่สิ่งที่สำคัญอย่างแท้จริง นั่นก็คือการเล่นเกมของคุณ ด้วยตัวเลือกการเดิมพันที่หลากหลายและการสนับสนุนลูกค้าที่เป็นเลิศ
ufabet 678 ไม่ว่าจะแทงบอล สล็อต หรือคาสิโนสด ทุกเกมมีโอกาสชนะสูง ทำกำไรแบบไม่ยั้ง
ufabet 678 แพลตฟอร์มเกมออนไลน์ชั้นนำที่ให้บริการเดิมพันหลากหลายรูปแบบ ไม่ว่าจะเป็นฟุตบอล สล็อต และเกมคาสิโนสด โดยแต่ละเกมได้รับการออกแบบมาอย่างพิถีพิถันเพื่อให้ผู้เล่นมีโอกาสชนะสูง รับรองประสบการณ์ที่น่าดึงดูดและคุ้มค่าทำให้เป็นตัวเลือกที่เหมาะสำหรับนักพนันทั้งมือใหม่และมือเก๋า ไม่ว่าคุณจะชอบเดิมพันกีฬาหรือเกมคาสิโน UFABET 678 รับประกันความตื่นเต้นและโอกาสทำกำไรมหาศาล
ufabet 678 เสิร์ฟประสบการณ์คาสิโนสด ส่งตรงจากบ่อนชั้นนำถึงมือคุณ เล่นได้ทุกที่ ทุกเวลา
ufabet 678 ด้วยแพลตฟอร์มที่ราบรื่นซึ่งให้คุณเล่นได้ทุกเมื่อทุกที่ ตอบสนองความต้องการของทั้งผู้เล่นที่มีประสบการณ์และผู้เล่นใหม่ บริการนี้รับประกันการสตรีมคุณภาพสูงและการเล่นเกมแบบโต้ตอบ นำความตื่นเต้นของการพนันแบบเรียลไทม์มาสู่ความสะดวกสบายในบ้านของคุณหรือขณะเดินทาง เกมแต่ละเกมจะจัดโดยดีลเลอร์มืออาชีพ ช่วยเพิ่มความถูกต้องให้กับประสบการณ์ของคุณทำให้เป็นตัวเลือกอันดับหนึ่งสำหรับผู้ที่ชื่นชอบคาสิโนออนไลน์ที่แสวงหาความสะดวกและคุณภาพ
ufabet 678 เล่นง่ายผ่านมือถือหรือคอมพิวเตอร์ พร้อมรับโปรโมชั่นเด็ดที่แจกหนักทุกวัน
ufabet 678 มอบประสบการณ์การเล่นเกมที่ราบรื่นซึ่งเข้าถึงได้ทั้งผ่านอุปกรณ์พกพาและคอมพิวเตอร์ ทำให้มั่นใจได้ว่าผู้ใช้สามารถเพลิดเพลินกับเกมโปรดได้ทุกที่ทุกเวลา แพลตฟอร์มได้รับการออกแบบมาโดยคำนึงถึงความเป็นมิตรต่อผู้ใช้ ช่วยให้ผู้เล่นสามารถนำทางผ่านข้อเสนอมากมายได้อย่างง่ายดาย นอกจากอินเทอร์เฟซที่ใช้งานง่ายแล้ว มีโปรโมชั่นประจำวันที่น่าดึงดูดใจซึ่งช่วยยกระดับประสบการณ์การเล่นเกมอย่างมาก โบนัสที่ใจป้ำเหล่านี้ไม่เพียงแต่ดึงดูดผู้เล่นใหม่เท่านั้น แต่ยังตอบแทนลูกค้าที่ภักดีอีกด้วย สร้างชุมชนเกมเมอร์ที่มีชีวิตชีวา ด้วยความมุ่งมั่นต่อคุณภาพและความพึงพอใจของลูกค้า
ufabet 678 ฝาก-ถอนทันใจ ได้เงินจริง รับกำไรแบบปังๆ ทุกวัน
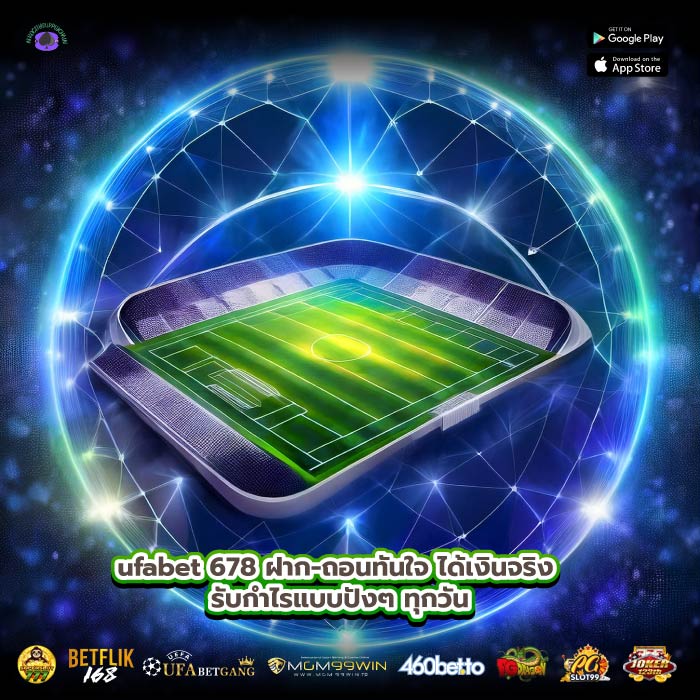
ufabet 678 ทำให้มั่นใจได้ว่าธุรกรรมจะได้รับการดำเนินการอย่างรวดเร็วและมีประสิทธิภาพ ด้วยการเน้นที่การมอบผลกำไรทางการเงินที่แท้จริง แพลตฟอร์มนี้ช่วยให้ผู้ใช้เพลิดเพลินไปกับผลกำไรมหาศาลทุกวัน อินเทอร์เฟซที่ใช้งานง่ายและฟีเจอร์ที่แข็งแกร่งตอบสนองความต้องการของนักเดิมพันทั้งมือใหม่และมือเก๋า ช่วยส่งเสริมสภาพแวดล้อมที่น่าดึงดูดสำหรับทุกคน ด้วยการให้ความสำคัญกับความพึงพอใจของลูกค้าและความปลอดภัยทางการเงิน จุดหมายปลายทางที่เหมาะสำหรับผู้ที่ต้องการผลตอบแทนจากการลงทุนที่มากพอสมควร
ufabet 678 ทุกเกมมาพร้อมโปรโมชั่นสุดพิเศษ เล่นง่าย จ่ายชัวร์ ไม่มีขั้นต่ำ แถมยังมีทีมซัพพอร์ต 24 ชม.
ufabet 678 โดยมีเกมให้เลือกมากมายพร้อมโปรโมชั่นพิเศษที่ช่วยเพิ่มการมีส่วนร่วมของผู้ใช้ ด้วยอินเทอร์เฟซที่ใช้งานง่าย ผู้เล่นสามารถนำทางแพลตฟอร์มได้อย่างง่ายดาย ทำให้มั่นใจได้ว่าจะได้รับประสบการณ์การเล่นเกมที่ราบรื่น ความมุ่งมั่นในความน่าเชื่อถือนั้นเห็นได้ชัดจากกระบวนการชำระเงินที่ตรงไปตรงมา ซึ่งดำเนินการโดยไม่มีข้อกำหนดการฝากเงินขั้นต่ำ ช่วยให้การจัดการทางการเงินมีความยืดหยุ่น ยังให้ความสำคัญกับการสนับสนุนลูกค้า โดยจัดให้มีทีมงานเฉพาะที่พร้อมให้บริการตลอด 24 ชั่วโมงเพื่อช่วยเหลือเกี่ยวกับคำถามหรือปัญหาต่างๆ แนวทางที่ครอบคลุมนี้เน้นย้ำถึงความมุ่งมั่นที่จะมอบสภาพแวดล้อมการเล่นเกมที่ปลอดภัยและสนุกสนานให้กับผู้ใช้ทุกคน
ufabet 678 เว็บตรงไม่ผ่านเอเยนต์ ครบจบในที่เดียว บอล คาสิโน สล็อต ยิงปลา
ถ้าคุณกำลังมองหาเว็บเดิมพันออนไลน์ที่ครบวงจรที่สุดที่นี่คือแหล่งรวมเกมเดิมพันครบจบในที่เดียว ไม่ว่าจะเป็น แทงบอล คาสิโนสด สล็อต บาคาร่า และเกมยิงปลา ทุกเกมเล่นได้ในยูสเดียว ไม่ต้องโยกเงินเดิมพันได้ทุกที่ทุกเวลาผ่านมือถือ รองรับทุกระบบทั้ง iOS และ Android มาพร้อมกับระบบฝาก-ถอนอัตโนมัติที่รวดเร็วใน 1 นาที การันตีความปลอดภัย 100% เล่นได้เท่าไหร่ ถอนได้เต็มจำนวน ไม่มีล็อกยูส สมัครสมาชิกวันนี้เพื่อรับโปรโมชั่นพิเศษ เครดิตฟรี และโบนัสจัดหนักให้กับสมาชิกใหม่เท่านั้น
FAQs คำถามที่พบบ่อย
ทำไม เข้าสู่ระบบ ufabet 678 ถึงได้รับความนิยมในหมู่นักพนัน?
นอกจากนี้ ufabet 678 ยังโดดเด่นด้วยระบบการจัดการที่ปลอดภัยและเชื่อถือได้ นักพนันสามารถมั่นใจได้ว่าการทำธุรกรรมทั้งหมดจะได้รับการปกป้องด้วยมาตรฐานความปลอดภัยสูงสุด การบริการลูกค้าที่ตอบสนองรวดเร็วตลอด 24 ชั่วโมงยังช่วยสร้างประสบการณ์การเดิมพันที่ราบรื่นและไร้กังวล
อีกทั้ง ufabet 678 ยังมีโปรโมชั่นและโบนัสต่าง ๆ ที่ออกแบบมาเพื่อเพิ่มโอกาสในการชนะของผู้เล่น สิ่งเหล่านี้ทำให้นักพนันรู้สึกว่าพวกเขาได้รับความคุ้มค่าในการลงทุนทุกครั้ง ด้วยข้อดีทั้งหมดนี้ จึงไม่แปลกใจเลยว่าทำไม ufabet 678 ถึงกลายเป็นเว็บไซต์ยอดนิยมสำหรับนักพนันทั่วโลก
การสมัครสมาชิกกับ ufabet 678 ไม่มีขั้นต่ำ มีขั้นตอนอย่างไรบ้าง?
เริ่มต้นด้วยการเข้าสู่เว็บไซต์หลักของ ufabet 678 แล้วมองหาปุ่ม “สมัครสมาชิก” ซึ่งจะอยู่บนหน้าแรกของเว็บไซต์ คลิกที่ปุ่มนั้นเพื่อเข้าสู่หน้าการลงทะเบียน
เมื่อคุณอยู่ในหน้าลงทะเบียนแล้ว ให้กรอกข้อมูลส่วนตัวของคุณตามที่ระบบต้องการ เช่น ชื่อ-นามสกุล เบอร์โทรศัพท์ และอีเมล ข้อมูลเหล่านี้จำเป็นสำหรับการยืนยันตัวตนและความปลอดภัยในการใช้งาน
หลังจากกรอกข้อมูลครบถ้วนแล้ว ระบบจะส่งรหัสผ่านชั่วคราวไปยังเบอร์โทรศัพท์หรืออีเมลของคุณ เพื่อใช้ในการยืนยันตัวตน เมื่อได้รับรหัสผ่านแล้ว ให้นำมากรอกในช่องที่กำหนดเพื่อดำเนินการขั้นตอนต่อไป
สุดท้าย เมื่อยืนยันตัวตนเรียบร้อย คุณสามารถตั้งค่ารหัสผ่านใหม่เพื่อใช้ในการเข้าสู่ระบบครั้งถัดไป จากนั้นเพียงแค่ล็อกอินเข้าสู่บัญชีของคุณ คุณก็พร้อมที่จะสนุกสนานกับเกมและการเดิมพันต่างๆ ที่ ufabet 678 มีให้บริการ
ด้วยขั้นตอนง่ายๆ เหล่านี้ การสมัครสมาชิกกับ ufabet 678 จึงไม่ใช่เรื่องยุ่งยากอีกต่อไป เตรียมพร้อมที่จะสัมผัสประสบการณ์การเดิมพันออนไลน์ที่ยอดเยี่ยมได้เลย!
การฝาก-ถอนเงินกับ สมัคร ufabet มือถือ สะดวกและรวดเร็วจริงหรือไม่?
ไม่ว่าจะเป็นการฝากเงินเพื่อเริ่มต้นการเดิมพันหรือถอนกำไรหลังจากชนะ การดำเนินการทุกขั้นตอนถูกออกแบบมาให้ใช้งานง่าย และใช้เวลาเพียงไม่กี่นาทีเท่านั้น อีกทั้งยังรองรับหลากหลายช่องทาง ไม่ว่าจะผ่านธนาคารในประเทศ หรือแอปพลิเคชันกระเป๋าเงินออนไลน์ ทำให้ผู้เล่นสามารถเลือกวิธีที่สะดวกที่สุดสำหรับตนเอง
สมัคร ufabet มือถือ มุ่งมั่นที่จะมอบประสบการณ์การใช้งานที่ดีที่สุดแก่ผู้เล่นทุกคน ดังนั้น หากคุณกำลังมองหาแพลตฟอร์มที่มีระบบฝาก-ถอนเงินรวดเร็วและเชื่อถือได้ สมัคร ufabet มือถือ คือตัวเลือกที่ไม่ควรมองข้ามอย่างแน่นอน